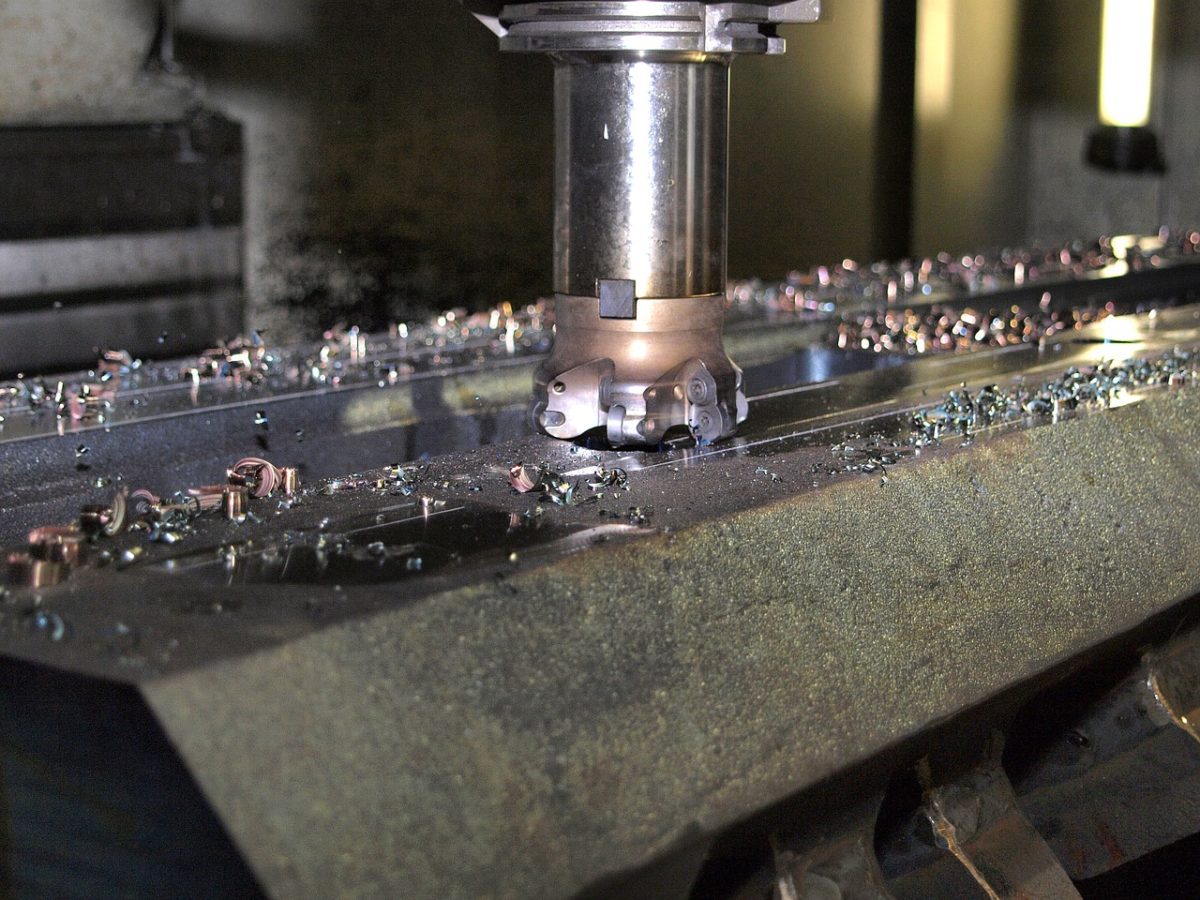
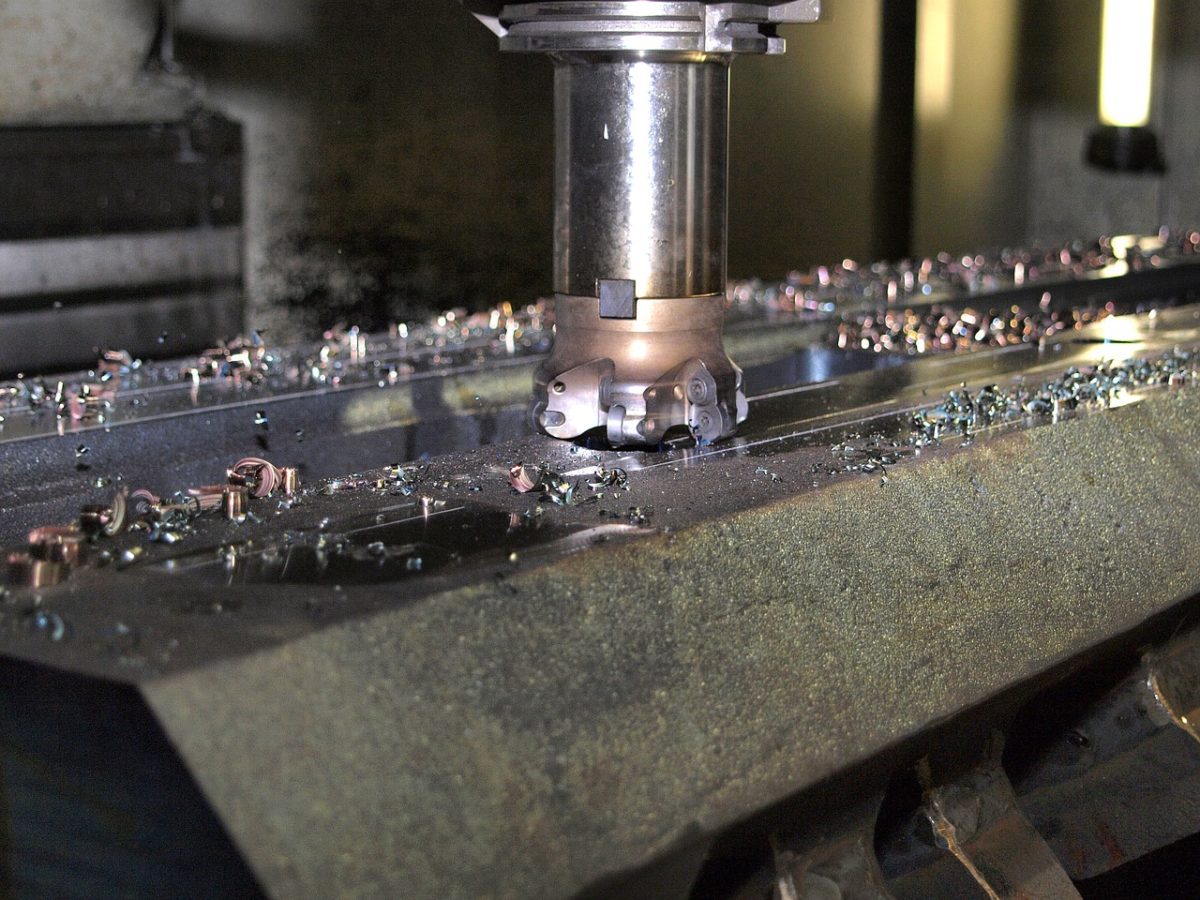
The preventive maintenance of machines and tools has the objective of prolonging the life of the machinery, as well as avoiding damage, failures and errors that could stop the production chain. In addition, of course, these maintenance plans also serve to protect the operators, as they improve the safety of the workshop.
What are the types of industrial maintenance?
Machine tools can also present failures, have errors, malfunctions, break down and have no repair. Any part of a machine can atrophy and stop the production chain, which would undoubtedly delay delivery times and mean losses for the factory or workshop. On the other hand, when a machine begins to fail, and if the failure is not addressed, it could become completely unusable and this would mean replacing it with a new one. This means an economic outlay.
And last but not least, failing machines put the safety of factory workers at risk. A machine that does not work as it should can cause fires, it can get stuck, lose fluid, not respond to operator orders to stop, and much more. This, without a doubt, translates into a danger for workshop workers.
Since machines were invented as we know them today, their maintenance was devised. Due to the task they perform, machine maintenance can be corrective, preventive and predictive.
Corrective maintenance
Preventive maintenance
When a machine breaks down, production stops until the equipment error is corrected. This can take a couple of hours, days, weeks, or require buying a new machine. To avoid corrective maintenance, a system was devised to reduce risks. Thanks to this series of tasks it is possible to prevent failures, errors, breakdowns in the equipment and their tools.
Predictive
Predictive maintenance makes use of statistical data to be able to predict errors that could occur in facilities and equipment.
How to do preventive maintenance of machines and tools?
In order to avoid equipment failures, it is important that maintenance technicians in workshops and factories carry out control inspections. Through these, they will verify that the machines are being used according to the indications of the manufacturer; And it is that one of the main errors is not making the proper use of machine tools.
During these routine inspections, the technicians must also control the state of the installations. In other words, that the workshop facilities are in optimal conditions for the machines to operate, such as, for example, that they receive adequate ventilation or that the electrical power is necessary. Thanks to these small actions, it is possible to extend the useful life of the equipment and avoid unexpected failures.
Types of preventive maintenance
Preventive maintenance can be done based on time; that is, daily, weekly, monthly or annual actions are scheduled to review the equipment and to be able to detect possible breakdowns. To carry out this type of maintenance it is important that there is planning and coordinationby all the departments of a workshop.
And it is that for preventive maintenance the machines have to be in use. It does not mean that they are working at the precise moment in which the inspection is carried out, but it does mean that they are operational machines, that work on a daily basis. Among the daily prevention tasks, we can mention the cleaning of shavings; as weekly work, the change or replenishment of oil.
Another type of preventive maintenance is the one based on the use of the machines. That is, if a machine is used daily, it should be monitored. To do this, the operators or maintenance technicians must keep a control of the hours of operation, the cycles of production, etc. For example, in factories where there are machines that are operating 24 hours a day, these must be checked frequently to avoid sudden breakdowns that stop production.
Develop the prevention strategy
Every machine tool is different. Not all need the same care to work, but it is true that there are some points in common, for example, cleaning. In the case of machines that start chips, remove these from the bed and other parts where chips can be stored. Oil should also be used to grease the moving parts of the machine and prevent their wear. Of course, the facilities must be impeccable and have the ideal environment so that these machines can work (electricity, water supply, oil, light, ventilation, temperature, etc.).
Each machine in the workshop must have its own preventive maintenance plan (weekly, monthly, yearly); Periodic inspections of the equipment should be scheduled, in addition to cleaning (ground and machine), monitoring the software strong>(in the case of CNC machines) and, of course, notify maintenance when a part does not work properly so that it can be replaced or repaired.