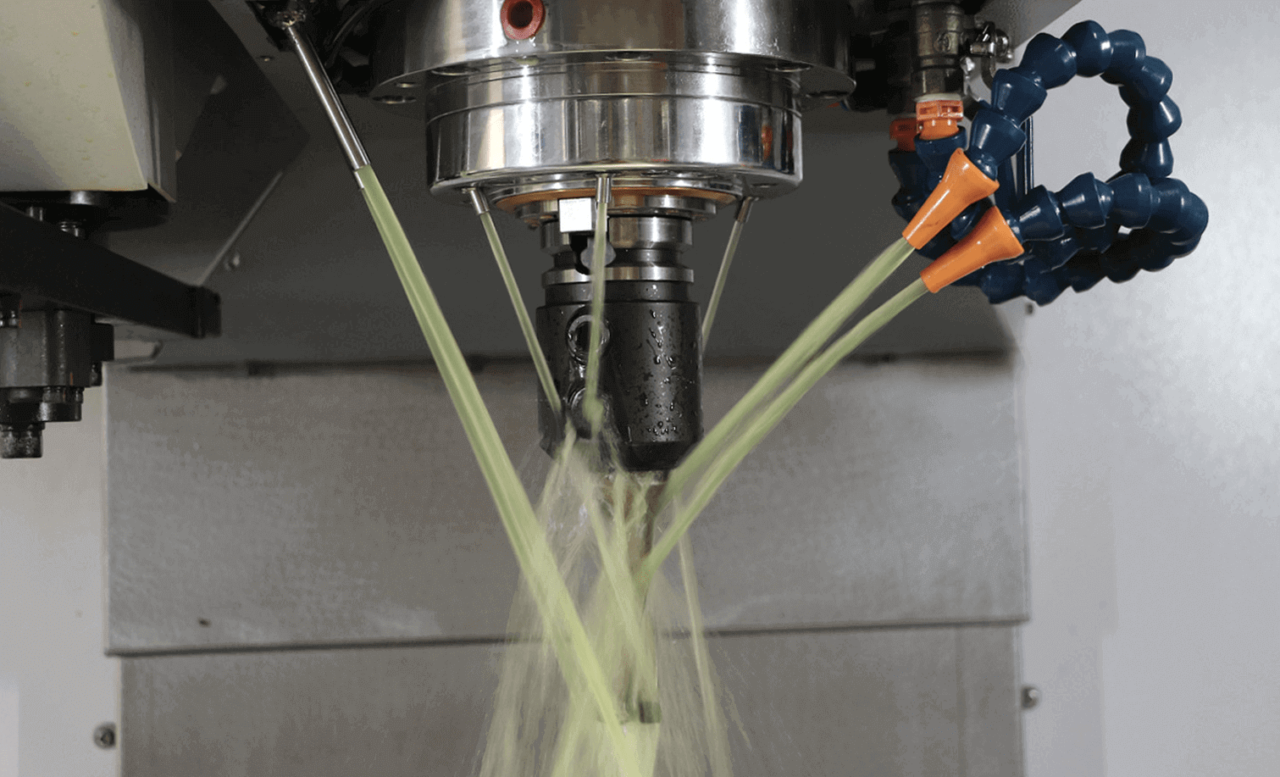
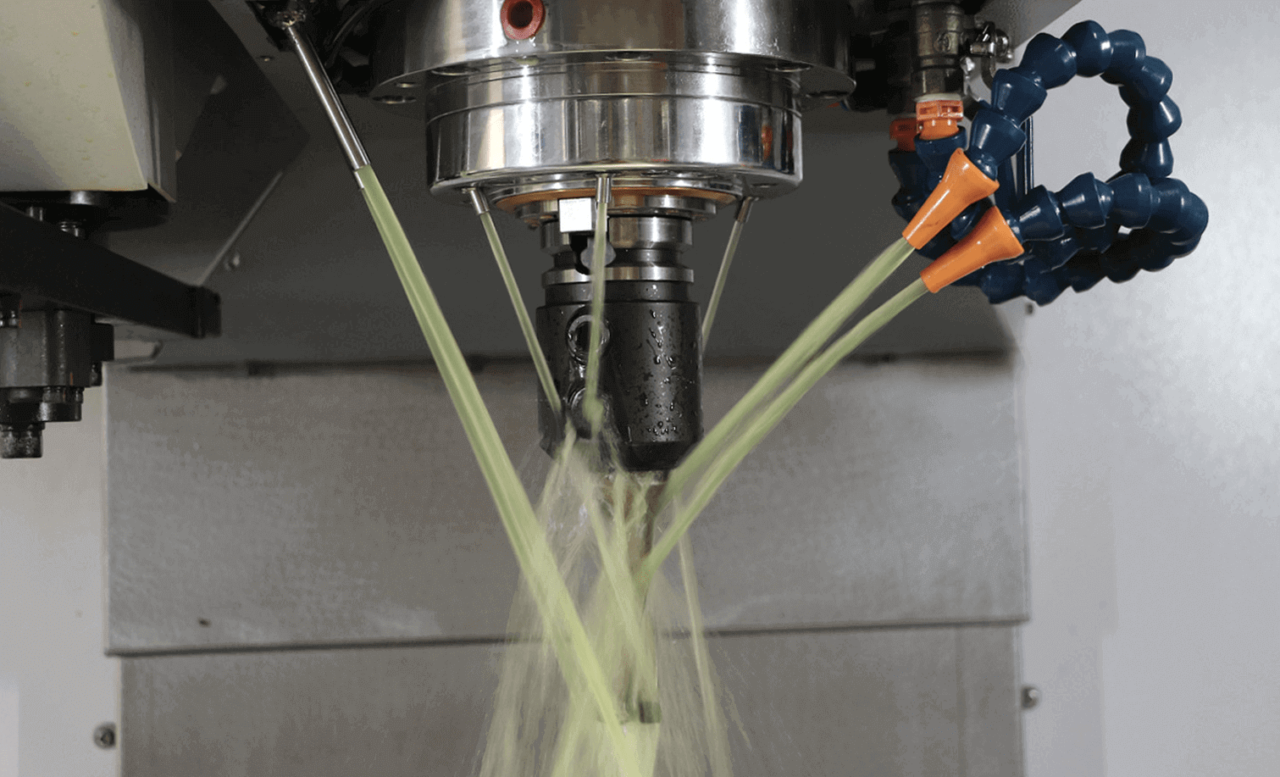
Los centros verticales son, en sí mismos, un tipo de centro de mecanizado. A grandes rasgos, existen otros dos tipos que son los centros horizontales y los centros tipo pórtico. Sin embargo, los verticales se encuentran entre los más usados y extendidos dada la gran cantidad de ventajas que presentan, lo que ha llevado al surgimiento de infinidad de modelos ajustados a cada necesidad industrial en fábricas y talleres de metalurgia.
A día de hoy, el tipo de centro vertical más común es el CNC (Control Numérico Computarizado), el cual destaca por funcionar de manera completamente automatizada: tan solo requiere de la programación de códigos equivalentes a las coordenadas que la herramienta debe seguir para realizar las tareas de mecanizado requeridas sobre una determinada pieza.
Características generales de un centro vertical
Los centros verticales, como ya dijimos, se presentan en infinidad de modelos, pensados para atender múltiples necesidades de mecanizado y en distintos sectores (un ejemplo es la industria automotriz). No obstante, las características generales de cada modelo son esencialmente las mismas:
Husillo vertical |
La principal característica es que el cabezal portaherramientas se encuentra ubicado en la parte superior de la máquina y su recorrido es vertical. En este sentido, la pieza de trabajo se mecaniza desde arriba hacia abajo. |
Automatización por CNC |
En la parte externa de la máquina se encuentra una pantalla con botones ingeniosamente pensados para facilitar la programación de códigos numéricos, coordenadas o instrucciones que serán procesados por un computador para llevar a cabo los movimientos necesarios en la herramienta hasta obtener los resultados deseados en la pieza mecanizada. Si los códigos están bien programados, el margen de error humano queda prácticamente anulado, alcanzando una precisión milimétrica en las distintas superficies de la pieza. |
Múltiples ejes |
Actualmente se siguen desarrollando centros verticales cada vez más avanzados, de forma que ahora se pueden encontrar modelos con múltiples ejes que permiten mecanizar la pieza desde distintos ángulos, lo que se traduce en la obtención de formas y geometrías más complejas. Estos ejes pueden estar ubicados en el cabezal y/o en la mesa de trabajo. |
Sistema de refrigeración líquida |
Las altas temperaturas que se producen por el roce de la herramienta con las piezas de trabajo son controladas por un sistema de refrigeración líquida. El líquido refrigerante se dispara mediante tubos que apuntan directamente sobre la superficie de las piezas, que además sirve para eliminar las virutas desprendidas. |
Torreta multi herramienta |
Los modelos más recientes también han incorporado sistemas automatizados para que el centro vertical sea capaz de cambiar las herramientas por sí mismo. Los sistemas más extendidos son dos: uno donde un brazo robótico remueve una herramienta del cabezal insertando otra, y uno donde la torreta tiene múltiples cabezales (cada uno con una herramienta ya montada) en una especie de disco giratorio. |
A propósito de esta última característica, cabe resaltar que estas máquinas-herramientas pueden desempeñar múltiples funciones, no solo la más tradicional que consiste en el fresado. Por ejemplo, también funcionan como un Centro de Roscado Vertical o como un Centro de Taladrado Vertical. Todo depende de la herramienta empleada para cada tipo de tarea requerida.
Ventajas de utilizar un Centro de Mecanizado Vertical
Los distintos tipos de centros verticales suponen múltiples ventajas a la hora de mecanizar piezas, sobre todo metálicas, cuyo modelado es difícil de hacer y consume grandes cantidades de tiempo bajo los métodos convencionales. De hecho, la reducción de tiempos y la facilidad de los procesos son dos de las principales ventajas que tienen los centros verticales. Además, están otros beneficios igualmente destacables:
- Maximizan la cantidad de producción a escalas masivas.
- Mejoran el rendimiento financiero de la fábrica o taller donde se usan.
- Se pueden montar distintos centros verticales en serie con la supervisión de uno o muy pocos operadores.
- Reducen costes en mano de obra y operarios.
- Proporcionan resultados extremadamente precisos, dejando las superficies lisas y libres de imperfecciones.
- La producción en serie es más precisa y homogénea entre las distintas unidades fabricadas.
- La pieza de trabajo se mecaniza desde arriba, lo que permite al operario ver más fácilmente el proceso y comparar los resultados con el diseño.
- Basta con programar los códigos necesarios para las distintas piezas y movimientos de mecanizado que se necesitan en un taller, para que luego solo deban ser intercambiados cada vez que se necesite.
- El cambio automático de las herramientas reduce enormemente los tiempos de producción, así como también las probabilidades de error humano.
Es importante aclarar que este tipo de máquinas-herramienta acarrean ciertas “desventajas”, dado que el beneficio económico a medio y largo plazo las compensa con creces. Las más destacables son su elevado coste inicial, así como los gastos en mantenimiento y reposición de componentes, que también son considerablemente altos.