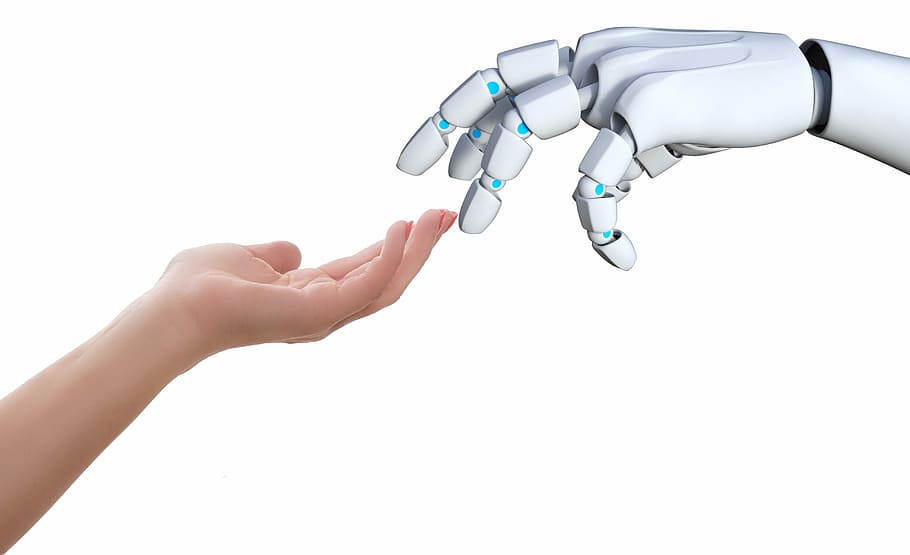
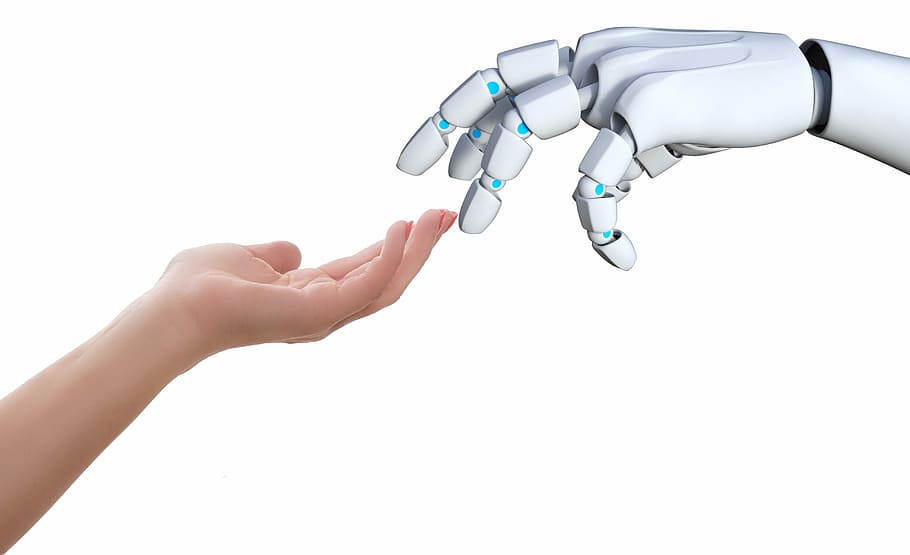
In recent years, robots have been changing the different sectors of the industry, until transforming it into the recent industry 4.0, a kind of revolution where artificial intelligence has a greater participation in production processes. One of the causes of this new industrial age is the so-called collaborative robotics.
Participation of robotics in the industry
Robotics is a science that encompasses various fields of technology and electronics; the objective of this discipline is to create machines capable of imitating certain human behaviors. The term robot was first coined and used in 1920; This is where the concept of machines capable of finishing the heavy work of factory laborers arose.
Although robots emerged as part of science fiction, it was precisely in these works of literature that the foundations of robotics were laid. Thus we find that a robot cannot harm humans; that robots must comply with a series of orders given by humans and, finally, they must ensure their existence as long as the first two principles do not conflict. Over the years, robots stopped being just something from science fiction and became tangible and quite real objects.
Thus , collaborative robotics was born, a part of robotics in which machines are created, with enough artificial intelligence to perform tasks in collaboration with humans. In this way, robots and humans work together to facilitate production processes.
Cobots: main actors of collaborative robotics
In collaborative robotics the main actors are the cobots; robots programmed to work together with humans in the so-called industry 4.0. Cobots, like all robots, must follow a series of safety regulations so that work is safe for factory workers and thereby reduce workplace accidents to a minimum.
It is important to clarify that a cobot is not the same as an android or a domestic robot. For example, cobots are designed for easy programming and have fairly simple operating systems; In addition, this programming can be regulated and adjusted according to the needs of the work. In this way, cobots can perform multiple tasks, while domestic robots (for example, the vacuum cleaner) are usually programmed for a single activity.
On the other hand, collaborative robotics machines are made of very light materials and use sensors that have the ability to stop the activity in case of detecting unusual movements that put the safety of the workers at risk. Finally, cobots allow the creation of tailor-made products according to what customers request; hence, it is essential that industry 4.0 workers have adequate training to be able to operate these machines.
Types of cobots
According to the International Federation of Robotics, there are two different types of cobots:
- Cobots that comply with the ISO 10218-1 standard, which meet the necessary requirements for safe work.
- Cobots that do not comply with the ISO 10218-1 standard, that do not have international standards, but have passed national or regional regulations. For example, cobots that may be valid in countries of the European Union, but not in the rest of the world.
Advantages of collaborative robotics in industry 4.0
The inclusion of collaborative robotics in factories brings nothing but benefits for the industry. To begin with, a cobot is capable of carrying out heavy work, quickly and efficiently, which allows operators to dedicate themselves to performing other types of tasks; all that is required is programming the cobot to tell it what to do. This, consequently, allows workers to release their workload.
In addition, the time it takes a cobot to perform a task means that the costs of the production process are considerably reduced, by not having to employ workers for long hours to produce a product. In other words, process times are reduced and it is a benefit for the client and also for the factory or workshop.
Cobots have the advantage of being very easy to program and operate, and they are also much cheaper than traditional automated machines. On the other hand, being made of light materials and having a fairly small size, the cobots can be easily transported.
Human-cobot relationship
No matter how much Artificial Intelligence a machine has, it will always be the human in charge of programming it to execute the tasks it has to perform. But can collaborative robotics replace workers? On the contrary, cobots are responsible for improving the productivity of operators and freeing them from tasks that are repetitive and can sometimes lead to injuries, to allow them to perform more complex tasks.
In the production process, the human contributes the ability to resolve conflicts, dexterity and flexibility; For its part, the cobot is responsible for providing strength, precision and resistance.