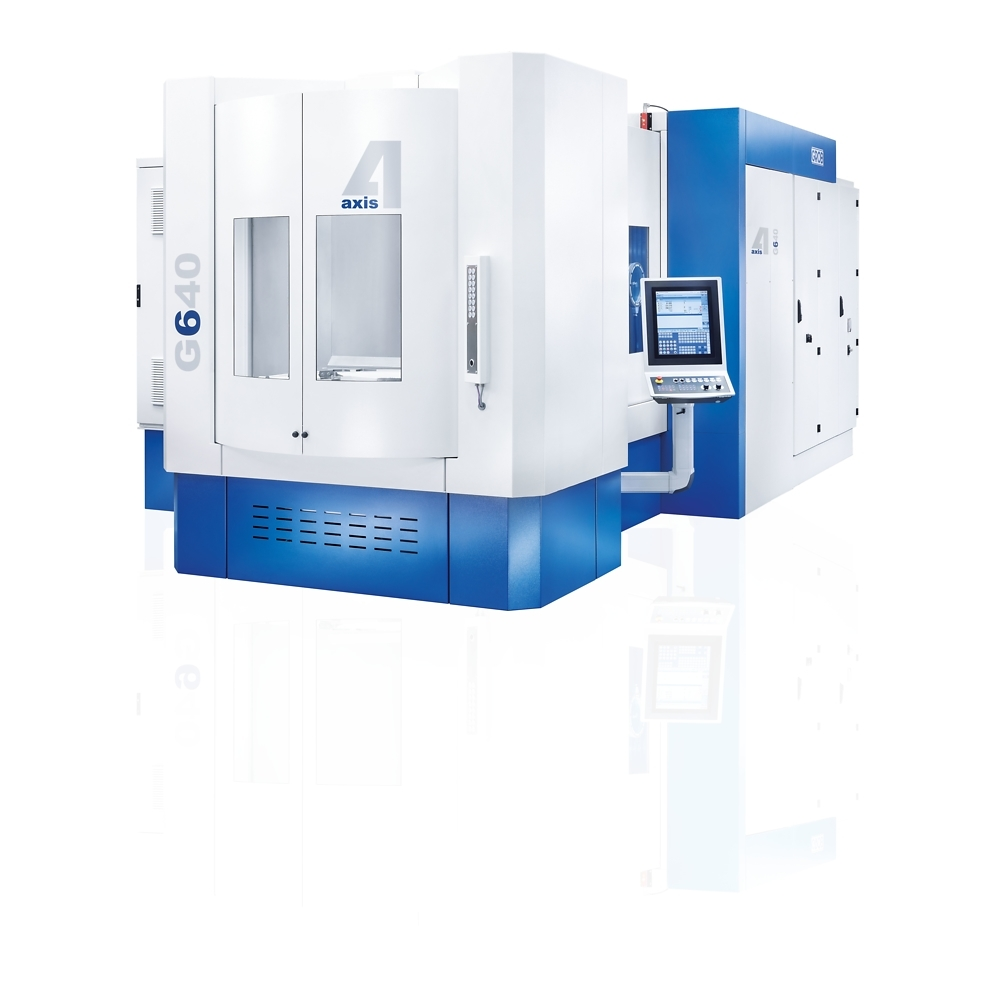
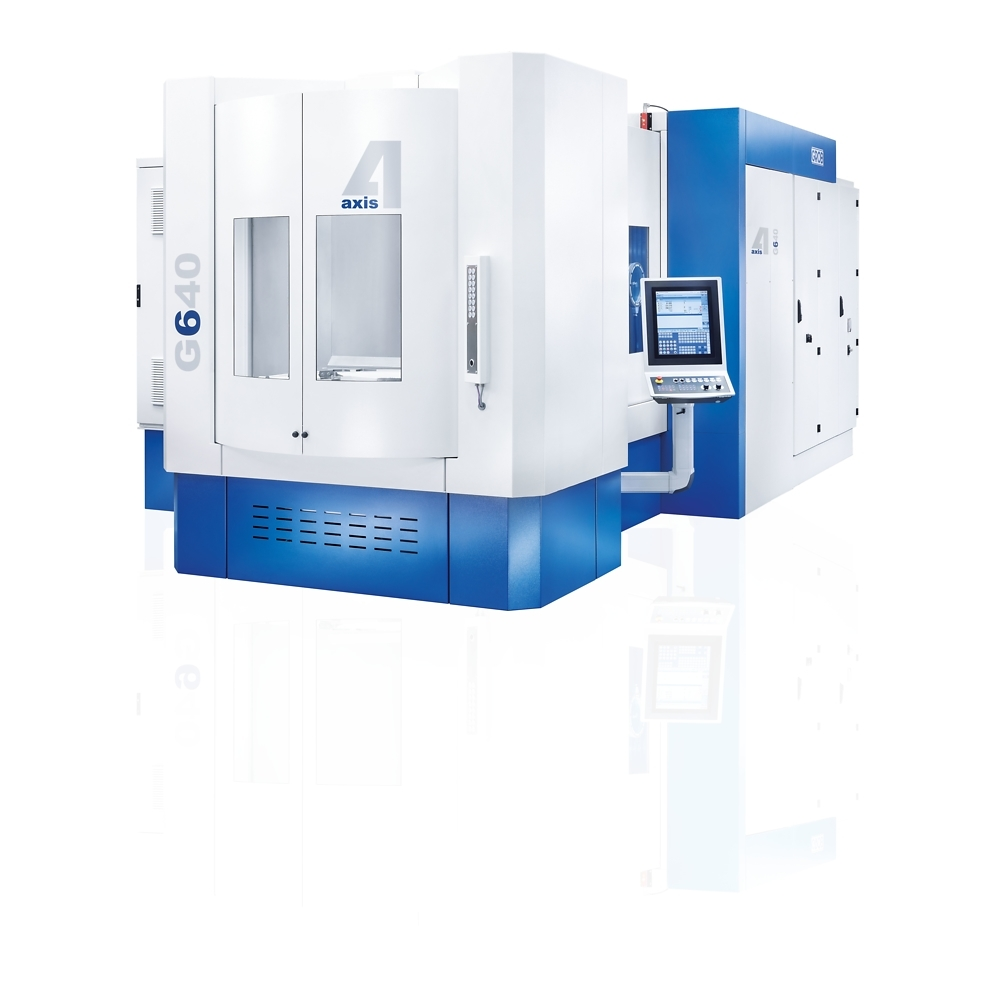
High -speed CNC machining or high-speed machining (HSM) is a method that allows working with parts in the metalworking industry and is characterized by increasing the efficiency, precision and quality of the parts. workpieces, when compared to conventional processes.
What is high speed machining?
This type of method, increasingly used in machining workshops, is used for the great benefits it brings. In addition to the fact that the parts are more precise and efficiency is increased, it is proven that this technique reduces production times and does not require much human intervention. This means that production costs are reduced considerably, but also delivery times.
High -speed machining is done using CNC computer numerical control technology; this means that the procedures are automated and require minimal operator intervention. But what is high speed CNC? We must specify that high-speed machining can be done in a single operation, but also in a combination of them, it all depends on the machine used.
This procedure can refer to cutting speed, spindle speed, feed rate, or chip removal rate. High-speed machining is characterized by the fact that the spindle reaches a speed of 3,000 to 6,000 revolutions per minute and a diameter of between 25 and 30 millimeters; In terms of speeds, it is important to highlight that these procedures are capable of machining with cutting speeds between five and ten times faster than by conventional methods.
In this type of machining, the depth and speed of the cut, as well as the feedrate, depend on the pieces to be worked on (shape, material, etc.).
High speed CNC applications
The type of material you want to work with plays a very important role in metalworking. It is not the same to machine an aluminum part as one made of steel or titanium; The hardness of the material itself also influences, as well as the dimensions of the piece to be worked on. But one of the great advantages of high-speed CNC is that it supports the machining of all types of parts. The versatility of the machines that support this machining has meant that they are used in different types of industries.
In addition to metalworking, high-speed CNC is used in the aerospace sector, but also in the manufacture of dies and molds. In both industries, very resistant metals are worked, such as titanium, stainless steel and aluminum. Let us remember that, for example, in the case of the elaboration of dies and molds, large volumes of these elements must be manufactured, that is, mass production and in large quantities. That is why it is highly advisable to machine at high speed.
Advantages of high speed machining
High speed CNC has many advantages for the metalworking industry. To begin with, it replaces machines of great depth at low cutting speed (something common in conventional machining), for others of lesser depth at higher speed; this causes the amount of chip removed to be greater. The cutting speed, being high, also reduces the cutting forces and the size of the chips.
Thanks to the fact that these cutting forces decrease, it is possible to machine very thin thicknesses, ranging from 0.2 millimeters. On the other hand, this type of machining allows for much greater precision in the contour and improves the quality of the surface of the part. The high-speed CNC makes it possible to evacuate almost all the heat generated during the process, through the chips and also reduces the coefficient of friction between the chips and the cutting tool.
Another advantage of this technique is that very hard steels can be machined and it also increases the useful life of the cutting tool. Finally, and as we already mentioned, production times are reduced, which minimizes delivery times; It does not require a large presence of operators, which also helps reduce production costs.
How should the machine be at high speed?
In order to obtain all the advantages of high-speed CNC machining, the machine and its tools must meet a series of requirements. The equipment must be capable of responding to the speeds required, as well as the profile that is to be achieved. On the other hand, the CNC integrated in the device has to have the quality of foreseeing how to change the trajectories of the cutting tools; for example, being able to switch between drilling and turning very quickly; or to be able to rotate the piece according to the desired angle.
The head tools have to be highly resistant to wear and suitable for the processes being carried out. Finally, for high-speed machining to work, it is essential to use CAM and CAD software that can create designs and strategies suitable for this type of machining.